Effect of nanographite on morphology, mechanical, dynamic mechanical, bound rubber and swelling studies of chlorobutyl elastomer nanocomposites
Shashi Kant Tiwari1, Bibhu Prasad Sahoo2 and Shyama Prasad Mahapatra1
1. Department of Chemistry, National Institute of Technology Raipur 492010 India.
2. Rubber Technology Centre, Indian Institute of Technology Kharagpur 721302 India.
Abstract
Nanographite reinforced chlorobutyl (CIIR) nanocomposites were prepared. The dispersion of the nanographite in the CIIR matrix has been investigated by SEM. The effect of increasing nanographite loadings (2, 4, 6, 8 phr) on mechanical properties like tensile strength, hardness, elongation at break and modulus (100%, 200%, 300%) has been studied. The study shows increase in tensile strength, hardness, modulus and decrease in elongation at break with nanographite loading, which can be attributed towards better CIIR-nanographite interaction. The above explanation was again verified from bound rubber measurements. It shows increase in bound rubber contents with nanographite loading. Dynamic mechanical analysis used to study their relaxation behavior as a function of temperature (-100oC to 100oC), at frequency 1 Hz and 1% strain. The effect of increasing nanographite loadings on glass transition temperature was marginal in all the composites and Tg value was in the range of -160C to-250C, which has been explained on the basis of relaxation dynamics of polymer chains in the vicinity of fillers. The effects of variation in nanographite loading and temperature on dynamic mechanical properties like loss tangent, storage and loss modulus has been reported. The effect of solvent (chloroform, benzene and tri-chloroethylene) on swelling properties at different period of time (15, 30, 45, 60 min.) shows that the degree of swelling increases with time & decreases with concentration of nanographite loading.
*Author for Correspondence:
Keywords: nanocomposite, mechanical, dynamic mechanical, bound rubber, swelling.
Introduction
For all practical applications (except adhesives), elastomers are reinforced with fillers to improve their performance by incorporating inorganic fillers. Traditionally this has been achieved by using materials such as carbon blacks, clays, talc and silica. But new generation fillers like carbon nanotubes, carbon silica dual phase filler, nanoclays and nanographite are continuously challenging the hegemony of these traditional fillers. The advantage of using nano scale fillers is their very high surface to volume ratio which leads to greater polymer-filler interactions thereby giving rise to significantly improved properties. Mechanical & dynamic-mechanical properties of composites reinforced with nano sized fillers show better properties than conventional micro-sized fillers. Decreasing size of the filler gives larger specific surface area thereby providing greater interactions between the polymer and filler leading to better properties. In recent years, there has been considerable research on nano particle based composites. Especially nanoclay reinforced plastics [1-3] and elastomers [4, 5] have been extensively studied. Graphite can provide additional advantages like excellent electrical and thermal conductivity. They also show good affinity for both organic compounds and polymers, therefore some monomers and polymers can be absorbed into the pores and galleries of graphite. Though there have been many studies on the effect of addition of nanographite in polymer matrix, it hasn’t been reported in elastomer matrices. The effect of type of fillers on the physico-mechanical properties and reinforcement of elastomer has been studied by many researchers [6-8]. Tripathy et al. [9] have reported the effects of types of carbon black on physical properties of elastomer in bromobutyl vulcanizates. Fillers also strongly influence the visco-elastic properties of elastomer compounds. The dynamic properties of elastomers filled with structural fillers are influenced by factors like type of fillers, volume fraction of filler, processing conditions and strain history. One of the consequences of the incorporation of fillers into a polymer is the creation of an interface between a rigid phase and a soft solid phase. Because of the interaction between the rubber and filler, the polymer molecules can be adsorbed onto the filler surface either physically or chemically. This adsorption leads to two phenomena, which are well documented: the formation of bound rubber (BdR) and a rubber shell on the filler surface. The phenomenon of BdR in rubber compounds has been studied extensively and is considered a typical feature of surface activity. BdR depends on filler characteristics like the surface area, structure or morphology, and surface activity [10-15]. The study of the swelling process and its kinetics, favor the estimation of the degree of cross-linking of a given polymer [16]. In fact the ability of polymers to dissolve or even swell is usually determined by many factors [17].
The objective of the present paper is to report the effect of addition of nanographite on properties of chlorobutyl nanocomposites. The dispersion of the filler in the polymer matrix has been studied by scanning electron microscopy. The effect of increasing nanographite loadings on the performance characteristics like tensile strength, modulus, hardness and elongation at break is also reported. The variation of the BdR content of nanographite filled chlorobutyl compounds was studied with the storage time using trichloroethylene, chloroform and benzene. Besides, the effect of nanographite loading on swelling study of chlorobutyl nanocomposites was also studied in above solvent. The relaxation behavior of nanographite reinforced chlorobutyl nanocomposites has been studied as a function of temperature (-1000
C to 1000
C) and frequency 1 Hz. The effects of variation in nanographite loading and temperature on dynamic mechanical properties like loss tangent, storage and loss modulus has been reported
.
EXPERIMENTAL
Materials
Cholorobutyl elastomer (CIIR, 1.25% chlorine content, Mooney viscosity ML 1+8 at 100°C =38) was procured from Bayer. Nanographite of purity ³ 95% were purchased from Nanoshel LLC, USA. Other chemicals like Zinc oxide of specific gravity of 5.4, Tetra Methyl Thiouram Disulphide (TMTD) having specific gravity 1.42 and compounding ingredients like sulfur, stearic acid were of chemically pure grade procured from standard suppliers.
Compounding and Sample Preparation
The rubber was compounded with the ingredients according to the formulations of the mixes (Table 1). Compounding was done in a brabender plastograph at 60 rpm followed by laboratory size (325x150 mm) mixing mill at a friction ratio of 1:1.25 according to ASTM D 3182 standards while carefully controlling the temperature, nip gap, time of mixing, and uniform cutting operation. The temperature range for mixing was 65–70°C. After mixing the elastomer compositions were molded in an electrically heated Moore Hydraulic Press at a pressure of 10 MPa and at 160 oC using moulding conditions determined by Monsanto Rheometer (R-100) according to ASTM D2084 and ASTM D5289 procedures.
Testing
Scanning Electron Microscopy
The particle size and morphology of the compounds has been studied by using INCA Penta FETX3-8113 (Oxford instruinment, England) Scanning Electron Microscope (SEM). Prior to SEM studies, the samples surface was sputter coated with gold. The fractured surfaces from tensile test were also studied by using INCA Penta FETX3-8113 (Oxford instruinment, England).
Mechanical Properties
Hardness of chlorobutyl nanocomposites were measured using a Shore-A Durometer as per ASTM D 676-59T. Mechanical properties like modulus, tensile strength and elongation at break according to ASTMD 412 procedure using dumbbell specimen were determined using a Hounsfield H10KS Universal Testing Machine. At least five specimens per sample were tested for each property and mean values are reported.
Bound rubber measurement
The contents of bound rubber (BdR) were determined by extracting the unbound materials such as the ingredients and free rubber with three different solvents for seven days followed by drying for two days at room temperature. The weights of the samples before and after extraction were measured, and the BdR contents were calculated using the following Equation
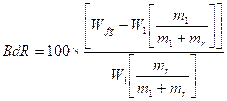
(1)
Where
BdR is the bound rubber content,

is the weight of filler and gel,

is the weight of sample,

is the fraction of filler in the compound and

is the fraction of rubber in the compound.
Swelling Studies
Swelling measurements of the nanocomposites (CIIR) were carried out using trichloroethylene, chloroform and benzene as solvents. Square samples of size 0.5mm and 0.3mm thickness were cut from the rubber sheets. Each sample is weighed by a sensitive balance. The test pieces were immersed in solvents, for different periods of time (15, 30, 45 and 60) wiped thoroughly and reweighed. It was found that, the equilibrium degree of swelling was attained after an immersion time of 24 hours. The degree of swelling was calculated according the relation

(2)
Where m0 is the weight of the unswelled sample, and m is its weight after swelling in solvent.
RESULTS AND DISCUSSION
Morphological Studies
SEM photomicrographs of the razor-cut surfaces of CIIR nanocomposites (2, 4, 6 and 8 phr nanographite) are presented in Figures 1(a-d). A comparison of the surface morphology shows a marked change in the properties at particular nanographite loading (8 phr). SEM studies reveals that the dispersion of nanographite is homogeneous in the polymer matrix but aggregation takes place as filler loading is increased, which is clearly observed from the SEM photomicrographs of samples containing 8 phr filler loading. This observation appears to be in good agreement with the results of mechanical properties. SEM micrographs shown in Figures 1a ,b, c and d at increasing nanographite concentration shows good distribution of in the elastomer matrix. Figures 2a, b, c and d show the fracture surfaces of the composite loaded with 2, 4, 6, 8 phr nanographite respectively. The fracture surface at lower nanographite loading is also relatively smooth and featureless, while a pronounced roughness was observed in the case of higher loading nanocomposite. Figure 2d shows the fracture surface of the 8 phr nanographite loaded sample at higher magnification. However it can be seen that the nanographite are well dispersed within the insulating elastomer matrix. Most of the fracture surfaces show spherical shaped dimples from pull out nanographite fillers. There is no obvious phase separation observed, implying good miscibility between elastomer and nanographite. At higher loading agglomerates acted as foreign body and initiate cracks in the composites under stress and also reduce elongation at break. Although the size of agglomerates were big but sphere-like agglomerate has lessen their effect as stress concentrator in composites, so, did not show pronounced effect on tensile properties and enhance the modulus. However, high amount of nanographite dispersed in elastomer matrix significantly increases the hardness and decreases the impact strength of the composite.
Mechanical Studies
Mechanical properties like tensile strength, elongation at break, modulus and hardness of the nanocomposites are shown in Table 2. From the table it is observed that Tensile strength, modulus (100%, 200%, 300%), hardness and thickness values increases with nanographite loading, while elongation at break decreases. The effect of incorporation of a nanographite (be it a reinforcing filler or not) on the mechanical properties of elastomeric materials can be partially explained as follows: If particles of high elastic-modulus are dispersed through a low elastic-modulus matrix, it is obvious that the modulus of the mixture will be higher than that of the matrix, mainly because of the decrease in volume content of matrix substance. However, for a filler to be really reinforcing in nature, many other factors come into the picture, the most important being the force of adhesion of the matrix to the particle. If the adhesion between the filler and the polymer matrix is very low then no significant increase in modulus (except due to hydrodynamic effect) can be observed. But, if the particle-to-matrix adhesive force is large, then the modulus of the mixture is primarily determined by the magnitude of the polymer-filler interactions. Increase in moduli is due to nanographite-rubber rigid interactions which are confirmed by bound rubber measurement. At 8 phr nanographite loading chlorobutyl gives the highest value of tensile strength, which means that at this loading elastomer-filler interaction is maximum. Unlike conventional filler, nanographite have very high surface area and this complex structure of the branched filler aggregates attributes to a strong surface polymer interaction leading to higher bound rubber content. Incorporation of fillers is a major source of energy dissipation thereby increasing the tensile strength of nanocomposites. On addition of filler like nanographite, free space between the chains is filled up, thus depriving the chains to straighten thereby reducing elongation. The higher the filler loading the more is the reinforcement and more crosslinks are formed during vulcanization, thereby trapping the free ends of polymer chains. As the degree of crosslinking increases, the hardness progressively increases. The more compact the networks, the shorter are the molecular segments between the crosslinks and hence the tighter is the network, which causes increase in hardness [18]. Very high value of hardness is due to highly reinforcing nanographite having very high surface area.
Bound Rubber Studies
Bound rubber can be defined as the rubber portion of uncured compound, which cannot be extracted by a good solvent due to adsorption of rubber molecules on to the filler surface. Bound rubber measurement plays an important role in determination of surface activity of the filler and the degree of reinforcement. It is widely accepted that the formation
of bound rubber in a compound involves physical adsorption, chemisorptions and mechanical interaction of which chemisorptions is considered as the crucial one. The adsorption of polymer molecules onto the filler surface leads to two phenomena, which are: the formation of bound rubber and a rubber shell on the filler surface. Many studies have been carried out on the mechanisms and factors affecting the formation of bound rubber [11–13]. The physico-chemical characteristics of the filler surface and filler morphology have a profound effect on the bound rubber content in a compound. The variation of bound rubber content with nanographite loading has been studied with three different solvents like benzene, trichloroethylene, and chloroform. Figure 3-5 shows effect of nanographite loadings on the variation of the bound rubber content of chlorobutyl nanocomposites as a function of the storage time in trichloroethylene, chloroform and benzene respectively. Irrespective of the nature of solvent, bound rubber content increases with nanographite loading due to increase in degree of reinforcement. The high percentage of BdR content is attributed to high surface area, high structure and high concentration of oxygen containing surface functional groups. High bound rubber values in sulfur added compounds have been reported earlier by Gessler [19]. The effect of type of solvent on the variation of the bound rubber content of chlorobutyl nanocomposites as a function of nanographite loadings is shown in Figure 6. The higher bound rubber content is observed from benzene than chloroform and trichloroethylene.
Dynamic Mechanical Studies
Effect of Temperature on Loss Tangent
Figure 7 shows the loss tangent spectra of CIIR composites, reinforced with increasing amounts of nanographite as a function of temperature. From the figure it can be observed that the location of maximum value of loss tangent (tan δmax) is not significantly affected by the extent of filler loading. All the samples show the glass transition in the narrow temperature range of -16 to -250C. This can be explained on the basis of relaxation dynamics of the polymer matrix. One of the main features of reinforced elastomers is that majority of polymer chains are in contact with the filler surfaces. Addition of filler into the polymer matrix induces a gradient of glass transition temperature in the polymer chains that are in the vicinity of the fillers due to the existence of strong dynamical heterogeneities [20, 21]. When a polymer is cooled through the glass transition region, the physical properties of the polymer in the non equilibrium state (at temperature lower than Tg), such as volume and enthalpy, gradually recover to new equilibrium values through the configurationally rearrangement of polymer segments. The rate of the rearrangement or relaxation process depends on the local environment surrounding the relaxation entities and hence reflects the extent of environmental restriction on those entities. But increasing filler loading shows decrease in the magnitude of the loss tangent with simultaneous broadening of the peak. The influence of filler on the damping behavior of filled polymer systems can be explained by two possible factors. One is a decrease in free volume which limits the mobility of molecular chains, usually in the case of elastomeric polymers, so that the damping value decreases. The other factor is an internal friction between the fillers and polymer chains, and between the filler particles themselves over the transition range, which increases with temperature, thereby causing greater movement of molecular chains so that the damping ability increases [22].
Effect of Temperature on Storage and Loss Modulus.
The variation in storage modulus (ε’) as a function of temperature (-100 to 100 oC) is shown in Figure 8. Irrespective of the nanographite loadings all the curves show characteristic sigmoidal variation of ε’ with temperature. The higher storage modulus with increase in nano graphite loading is due to formation of more filler network and also because of the decrease in volume content of base polymer. The effect of incorporation of a filler (be it a reinforcing filler or not) on the mechanical properties of elastomeric materials can be partially explained as follows: if particles of high elastic modulus are dispersed through a low elastic modulus matrix, it is obvious that the modulus of the mixture will be higher than that of the matrix, solely because of the decrease in volume content of matrix substance. However, for a filler to be really reinforcing in nature, many other factors come into the picture, the most important being the force of adhesion of the matrix to the particle surface which plays a crucial role. . The temperature dependence of loss modulus (ε") for various nanographite loadings is shown in Figure 9. A distinct transition peak at -25 oC may be attributed to the motion of methyl group directly attached to the backbone of CIIR. Incorporation of nanographite has some effect on the location and intensity but the amount of nanographite does not affect the temperature at peak, however the intensity slightly increases. Higher filler loadings result a percolated network of filler particles that can influence relaxation on a different scale
Cole-cole plots
The relaxation dynamics can also be expressed in terms of cole-cole plots i.e. relationship between storage and loss modulus. Cole–Cole plots for chlorobutyl nanocomposites are shown in Figure 10. Irrespective of nanographite loading at all concentrations of the filler, the usual depressed semi-circular can be observed which clearly indicates the presence of a reinforcing element. The large change observed on the arc radius in the Cole–Cole plot indicates the relaxation dynamics and a significant alteration of chain conformation due to nanographite interaction (23).
Relationship between Loss Tangent and Storage Modulus
Medalia and Laube reported the following simple relation between
and storage modulus (
) for natural rubber at 10% DSA at 25
C:
(3)
The dynamic mechanical properties of polymeric system may show different types of dependence with one another, especially when fillers are incorporated. A linear relationship between
and
was also established by Namboodiri for carbon black filed EPDM vulcanizates. Figure 11 shows the plot of
as a function of
with variation of nanographite loading. The linear nature of the plot could be mathematically expressed as
(4)
Where m is the slope of the line and C is a constant.
Swelling Studies
The formation of physical and chemical cross-linking between macromolecules through nanographite can be measured from cross-linking density. The swelling process and its kinetics, favors the estimation of the degree of cross-linking of a polymer. The degree of swelling increases progressively with time, especially at low concentration of nanographite hence a sharp rise in “Q” appears at the early stage of swelling. This sharp value is smothered as the nanographite increases and shifts to higher times. This could be explained in terms of the catastrophic rupture of the elastomer network due to the increase of internal stress caused by the diffused liquid i.e. internal stress is high compared with the force between macromolecules. By increase of filler, which is considered as high reinforcement filler, the formation of aggregates increases the force between macromolecules by forming a physical bond (adhesive) and resists the effect of internal stress of liquid, so such anomaly in “Q”% with time (t) disappears at higher concentration of nanographite. Figure 12-14 represent the time dependence of degree of swelling for chlorobutyl elastomer loaded with different concentration of nanographite in benzene, chloroform and trichloroethylene respectively. It is noticed from the three figures that, the value of the degree of swelling in trichloroethylene is smaller than chloroform and benzene. This is due to the high molecular weight of trichloroethylene. Figure 15 represent the dependence of the degree of swelling on nanographite concentration in chloroform, trichloroethylene and benzene after 30 minutes. It was noticed that the degree of swelling decreases with increase in nanographite loading. This means that, the molecular weight between two successive cross-links decreases [24].
Conclusions
Morphology shows good distribution of nanographite in chlorobutyl composites. Mechanical Properties like tensile strength increase with nanographite loading up to 8 phr. Elongation at break gradually decreases with nanographite loading due to better reinforcement. With nanographite loading hardness also gradually increases which may be due to increase in crosslink density. Irrespective of the solvent the bound rubber content increases with increase in the nanographite content. Very high value of bound rubber is due to high reinforcement obtained due to high structure and high surface area of nanographite. Solvents with more interaction with the polymer tend to show lower BdR values. The initial increase in BdR values in the first 15 days of storage was remarkable, after which there was only a slight increase. The dynamic mechanical analysis of the nanocomposites shows that the addition of the filler has no significant effect on the glass transition temperature (Tg). However on increasing nanographite loading the intensity of tan δ curve decreases. This has been explained in terms of filler-polymer interaction and inters aggregate interactions. Broadening of the relaxation region was observed in the plots of storage and loss modulus with temperature. Dynamic mechanical studies also show increase in storage modulus and dependent loss modulus shows a marginal effect on location and intensity, but does not change the temperature of the peak. The complete semicircular cole-cole plots confirm the non-linear/non-Debye type of relaxation in CIIR nanocomposite. Irrespective of MWCNT loading smoothness of the curve indicates well dispersion of MWCNT in chlorobutyl matrix. The degree of swelling increases with time but decreases with nanographite loading.
References
- Park HH and Jana SC, The relationship between nano and micro-structures and mechanical properties in PMMA-epoxy-nano clay composites, Polymer, (2003) 44, 2091.
- Usuki A, Kojima Y, Kawasumi M ,Okada A, Fukushim Y, Kurauchi T and Kamigaito O, Synthesis of nylon 6-clay hybrid, J. Mater. Res., (1993) 8, 1179.
- Alexandre M and Dubois P, Polymer-layered silicate nanocomposites: preparation, properties and uses of a new class of materials, Mater.Sci. Engng., (2000) 28, 1.
- Mousa A, and Karger-Kocsis, Rheological and Thermodynamical Behavior of Styrene/ButadieneRubber-OrganoclayNanocomposites, J. Macro. Mater. Engg., (2001) 286, 260.
- Sur GS, Sun HL, Lye SG and Mark JE, synthesis,structure,mechanical properties and thermal stability of some polysulfone/organoclay nanocomposites, Polymer, (2001) 42, 9783.
- Dutta NK, Tripathy DK, Effect of plasticizer concentration on the hysteresis, tearstrength an stress relaxation characteristics of black-loaded rubber vulcanizates, Colloid and Polymer Science, (1991) 269, 331.
- Shanmugharaj AM, Bae JH, Lee Noh KY, Lee WH, Ryu SH, Comp SH, Physical and chemical characteristics of multiwalled carbon nanotubes functionalized with aminosilane and its influence on the properties of natural rubber, Composites. Sci. Tech., (2007) 67, 1813.
- Fakhrul-Razi A, Atieh MA ,Girun N, Chuah TG, El- Sadiq M, Biak DRA, Effect of multi-walled carbon nanotubes on the mechanical properties of natural rubber, Comp. Stru, (2006) 75, 496.
- Dutta NK and Tripathi DK, Effects of types of fillers on the molecular relaxation characteristics, dynamic mechanical, and physical properties of rubber vulcanizates, J. Appl. Polym. Sci., (1992) 44, 1635.
- Stickney PB, Falb RD, Carbon black-rubber interactions and bound rubber, Rubber Chemistry and Technology, (1964) 37, 1299.
- Sircar AK, and Voet A, Immobilization of elastomers at the carbon black particle surface, Rubber Chem Technol., (1970) 43, 973.
- Wolff S, Wang MJ, Tan EH, Filler-elastomer interactions Part VII Study on bound rubber, Rubber Chem Technol., (1993) 66, 163.
- Kraus G, Reinforcement of elastomers by carbon black in ‘Advances in Polymer Science’ (eds.: Bunde A., Havlin S.) Springer Berlin, Heidelberg, Adv. Polym. Sci., (1971) 8, 155.
- Donnet JB, Rigaut M, Frustenberger R, Study by electronic paramagnetic carbon black resonance treats by the azodiisobutyronitrile in absence of oxygen, Carbon, (1973) 11, 153.
- Sridhar V, Gupta BR, Tripathy DK, Bound Rubber in chlorobutyl compounds: Influence of filler type and storage time, Journal of Applied Polymer Science, (2006) 102 , 715.
- Buchdahl R, Nielsen LE, The Application of Nutting's Equation to the Viscoelastic Behavior of Certain Polymeric Systems, J. Appl. Phys., (1951) 22, 1344.
- Barbara Barr-Howell D and Nikolaos Peppas A, Dynamic and equilibrium swelling of DVB-crosslinked polystyrene particles, J. Appl. Polym. Sci., (1985) 30, 4583.
- Chakraborty SK, Bhowmick AK and De SK, Mixed cross-link systems in elastomers, Polymer Reviews, (1981) 21, 313.
- Gessler AM, Evidence for chemical interaction in carbon and polymer associations: Extension of original work on effect of carbon black structure, Rubber Chemistry and Technology. (1969) 42, 858.
- Pham JQ, Mitchell CA, Bhar JL, Tour JM, Krishanamoorti R, Green PF, Glass transition of polymer/single-walled carbon nanotube composite films, J. Polym. Sc. Part B, Polym. Phy., (2003) 41 (24), 3339.
- Ediger MD, Spatially heterogeneous dynamics in supercooled liquids, Annu. Rev. Phys. Chem., (2000) 51, 99.
- Trakulsujaritchok T and Hourston DJ, Damping characteristics and mechanical properties of silica filled PUR/PEMA simultaneous interpenetrating polymer networks, Eur. Polym. J., (2006) 42, 2968.
- Valentini L, Amentano I, Biagotti J, Kenny JM, Santucci S, Frequency dependent electrical transport between conjugated polymer and single-walled Carbon nanotubes, Diamond & Related Materials, (2003) 12, 1601.
- Abdel-Ghani S A, Madkour TM, Osman, HM and Mohamed AR, Study of the electrical properties and swelling mechanism in compressed butyl rubber loaded with carbon black, Egypt. J. Sol., (2000) 23, 307.
Tables
Table- 1 Formulation of unfilled and MWCNT reinforced nanocomposites
Ingredient |
CB1 |
CB2 |
CB3 |
CB4 |
CB5 |
Chlorobutyl Rubber |
100 |
100 |
100 |
100 |
100 |
Nanographite(phr) |
0 |
2 |
4 |
6 |
8 |
Each mix contains ZnO 5 phr, Stearic acid 2 phr, TMTD 1 phr and Sulphur 1.5 phr.
Table 2 Mechanical properties of unfilled and MWCNT reinforced chlorobutyl nanocomposites
Mix
no. |
Thickness
(mm) |
Hardness
(shore A) |
Tensile
strength
(Mpa) |
Elongation
at break
(%) |
Modulus
(100%)
MPa |
Modulus
(200%)
MPa |
Modulus
(300%)
MPa |
CB1 |
2.32 |
32 |
5.73 |
513.5 |
1.2 |
2.3 |
3.63 |
CB2 |
2.40 |
38 |
8.25 |
952 |
2.6 |
3.5 |
7.4 |
CB3 |
2.47 |
40 |
10.04 |
820 |
4.9 |
5.8 |
9.1 |
CB4 |
2.60 |
45 |
12.54 |
760 |
6.5 |
8.3 |
9.6 |
CB5 |
2.78 |
51 |
17.03 |
745 |
8.5 |
9.3 |
12.8 |
Table 3 Bound rubber content as a function of nano graphite loading in chlorobutyl nanocomposites for different solvent after 15 days.
Nano graphite concentration |
Trichloroethylene |
Chloroform |
Benzene |
2 phr |
40.2 |
49 |
56 |
4 phr |
47.8 |
53 |
61 |
6 phr |
49.2 |
57 |
65.8 |
8 phr |
52 |
59.5 |
67.6 |
Figures
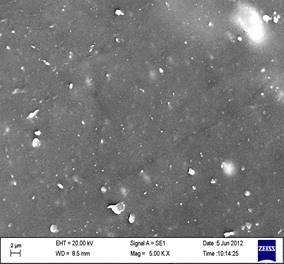
- 2 phr nano graphite (b) 4 phr nano graphite
(c) 6 phr nano graphite (d) 8 phr nano graphite
Figure 1 State of dispersion of nanographite in chlorobutyl elastomer: (a) 2 phr nanographite (b) 4 phr nanographite (c) 6 phr nanographite and (d) 8 phr nanographite.
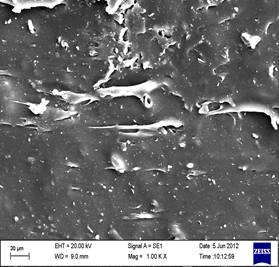
- 2 phr nano graphite (b) 4 phr nano graphite
(c) 6 phr nano graphite (d) 8 phr nano graphite
Figure 2 Fractographs of (a) 2 phr (b) 4 phr (c) 6 phr and (d) 8 phr nano graphite loaded filler agglomerates initiate crack during tensile deformation.
Figure 3 Effect of nano graphite loadings on the variation of the bound rubber content of chlorobutyl nanocomposites as a function of the storage time in trichloroethylene.
Figure 4 Effect of nano graphite loadings on the variation of the bound rubber content of chlorobutyl nanocomposites as a function of the storage time in Chloroform.
Figure 5 Effect of nano graphite loadings on the variation of the bound rubber content of chlorobutyl nanocomposites as a function of the storage time in benzene.
Figure 6 Effect of solvent on the variation of the bound rubber content of chlorobutyl nanocomposites as a function of nano graphite loading.
Figure 7 Variation of loss tangent (Tan δ) with temperature in chlorobutyl nanocomposites reinforced with nano graphite at increasing loadings.
Figure 8 Variation of storage modulus with temperature in chlorobutyl nanocomposites reinforced with nano graphite at increasing loadings.
Figure 9 Variation of loss modulus with temperature in chlorobutyl nanocomposites reinforced with nano graphite at loadings.
Figure 10 Cole-cole plots (storage modulus versus loss modulus) of chlorobutyl nanocomposites with increasing nanographite loadings.
Figure 11 Plots of Loss tangent (
) versus Storage modulus in chlorobutyl nanocomposites reinforced with nano graphite at increasing loadings.
Figure 12 Effect of nano graphite loading on degree of swelling as a function of time in Benzene.
Figure 13 Effect of nano graphite loading on degree of swelling as a function of time in Chloroform.
Figure 14 Effect of nano graphite loading on degree of swelling as a function of time in trichloroethylene.
Figure 15 Effect of solvent on degree of swelling after 30 minutes as a function of nano graphite loading.